The Advancement of Steel Marking Procedures: Innovations and Applications
The world of metal marking procedures has actually witnessed a transformative journey marked by consistent innovation and adjustment to satisfy the demands of modern commercial practices. From the conventional methods deeply rooted in history to the advanced modern technologies driving high-speed accuracy, the advancement of steel stamping has actually been absolutely nothing except remarkable. As brand-new tooling techniques and automation find their way right into this sector, the implications for efficiency and high quality are extensive. The applications span across a spectrum of markets, each benefiting uniquely from the developments in steel marking procedures.
Typical Metal Marking Methods
Traditional steel marking methods have long been the structure of manufacturing processes in numerous markets due to their performance and accuracy. The procedure includes forming a metal sheet or coil into a wanted shape by pushing it between a die and a punch. This approach is extensively made use of for creating huge quantities of parts with high precision at a fast pace.
One of the essential advantages of traditional steel stamping methods is the capability to preserve tight tolerances, guaranteeing that each part satisfies the needed specifications consistently. This degree of accuracy is essential in markets such as auto, aerospace, and electronic devices, where also small discrepancies can lead to significant problems.
In addition, traditional steel marking strategies supply cost-effective services for automation contrasted to other producing methods. The ability to stamp parts in fast sequence decreases production time and decreases labor prices, making it an appealing alternative for services looking to optimize their production processes.
Emergence of High-Speed Stamping
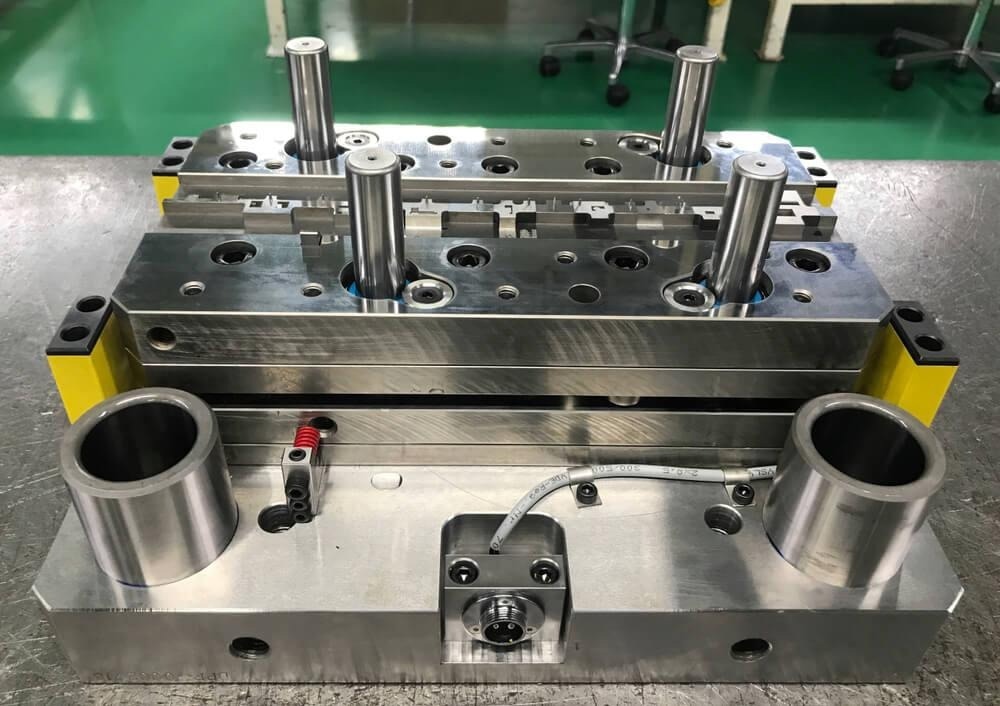
Among the key benefits of high-speed marking is its capability to keep precision and uniformity even at sped up handling speeds. This precision is crucial in markets where limited tolerances and complex layouts are required. In addition, high-speed stamping enables the handling of a wide variety of products, consisting of aluminum, stainless-steel, click here to find out more and copper, more expanding its applicability across numerous sectors.
Additionally, the introduction of high-speed marking has allowed makers to fulfill the growing demand for complicated parts in sectors such as automotive, aerospace, and electronics (Metal Stamping). By leveraging the speed and precision of high-speed marking modern technology, companies can enhance their competitiveness in a quickly progressing market landscape
Innovations in Tooling Technology
With the development of high-speed stamping enabling boosted accuracy and effectiveness in metal creating procedures, the field of steel marking has seen substantial advancements in tooling modern technology. Tooling innovation plays a vital function in steel marking operations, affecting aspects such as product top quality, production speed, and total cost-effectiveness.
By using these sophisticated products, tooling manufacturers can produce dies and mold and mildews that hold up against the high pressures and temperatures included in metal marking procedures, resulting in longer device life and improved production effectiveness. Generally, these innovations in tooling modern technology have transformed the metal stamping market, enabling suppliers to achieve higher levels of precision, productivity, and cost savings.
Combination of Automation in Stamping
As automation remains to reshape the landscape of metal stamping processes, the integration of automated systems has come to be significantly widespread in modern production facilities. Automated systems use countless advantages in steel marking, consisting of boosted effectiveness, enhanced accuracy, and enhanced safety. By including automation right into marking processes, producers can reduce cycle times, minimize product waste, and Find Out More enhance production throughput.
One of the vital elements of automation in stamping is making use of robot arms for tasks such as product handling, part adjustment, and high quality evaluation (Metal Stamping). These robotic systems can do repetitive and labor-intensive jobs with speed and accuracy, liberating human drivers to concentrate on even more complicated procedures. Furthermore, automation enables real-time tracking and adjustment of stamping procedures, resulting in greater general procedure control and quality guarantee
Furthermore, the combination of automation in stamping allows manufacturers to accomplish regular part top quality, meet tight this page resistances, and enhance general performance. As technology proceeds to advance, the function of automation in steel marking processes is anticipated to expand additionally, driving technology and effectiveness in the production industry.
Applications Across Diverse Industries
Incorporating steel marking processes throughout varied industries showcases the versatility and flexibility of this production method. Additionally, the device market advantages from metal stamping procedures to manufacture components for refrigerators, washing equipments, and other house home appliances. The adaptability of steel stamping procedures makes it a useful manufacturing method across different industries, showing its significance in modern-day production procedures.
Conclusion
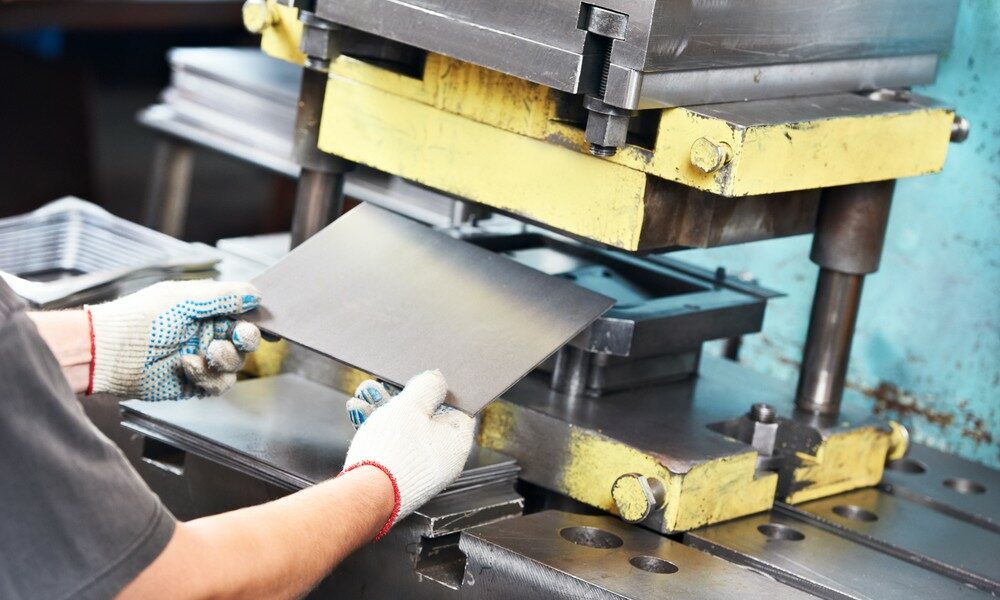